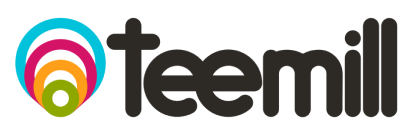
Teemill is a tech-based fashion business that takes a more holistic view of the fashion industry, designing out waste at each step of the material supply chain, applying disruptive technology to minimise overstocking, and maximise material recycling.
By opening up access to its circular supply chain platform, Teemill has allowed tens of thousands of brands to produce t-shirts in real time after they’re ordered, all designed to be sent back and remade when they’re worn out.
Why it’s an example of the circular economy
Teemill has developed a circular production process that turns old t-shirts into new ones and regenerates natural systems. Their approach starts by viewing the fashion supply chain as a connected system, then applies circular design principles and new technology across the product life cycle to reduce waste.
The Teemill supply chain increases material utilisation, reduces chemical and water inputs, removes barriers to entry in the fashion industry and means anyone with an internet connection can participate and co-create the future of fashion. New brands get the same systems as a mature brand for free, without surplus production.
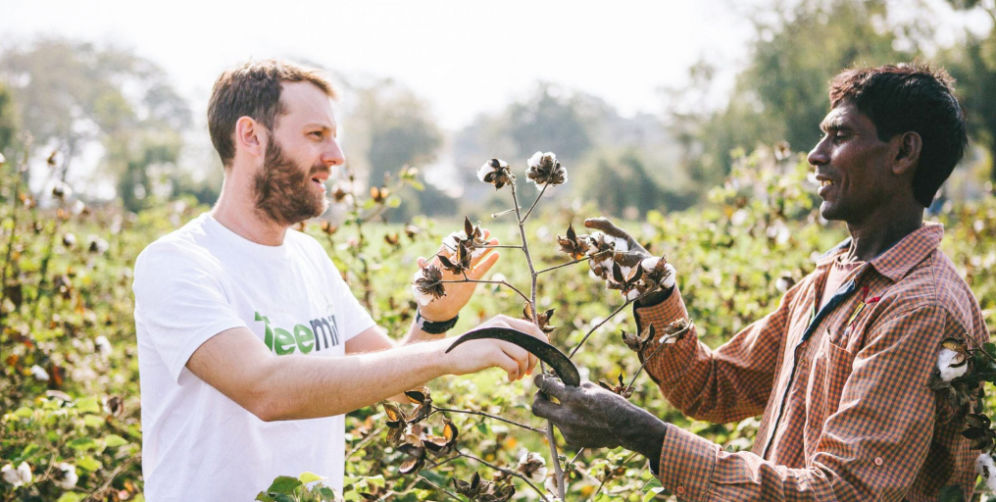
Image from Teemill
The production process
The Teemill circular story begins in farms in Northern India, where cotton is grown using organic fertilisers, irrigated through rainwater harvesting, and protected using insect traps rather than chemicals. Co-planting with other crops also helps fix nutrients and assists with pest control.
Harvested cotton is then transported to mills to separate raw materials, and spin the cotton fibres into useful material. The process generates by-products, including seeds that are turned into seed cakes, that are used to make vegetable oil and feed for cattle. This creates extra value, and returns nutrients to the natural system.
The transformation of textiles into garments often causes pollution, so much so that NGO China Water Risk estimates that 17 - 20% of industrial water pollution in China is caused through this process. To address this, Teemill’s factories recover, clean, and recirculate processed water, so that any discharged from the factory is good enough to drink. The plant where garments are cut and sewn is powered by renewable energyrenewable energyEnergy derived from resources that are not depleted on timescales relevant to the economy, i.e. not geological timescales., displacing fossil use and eliminating any carbon emissions.
Reducing waste with real-time printing
Products are made in real time - seconds after they’ve been ordered, so they only make what's needed and there's no waste. This means that a customer places an online order, specifying a colour, size, and design. The t-shirt is then printed a few seconds after the order is placed and sent out to the customer. In this way, the final product is only produced when it is needed.
Using machine-to-machine communications technology allows Teemill to turn equipment on only when necessary– this same technology automates a supply chain for start-ups, brands, and charities, all of which connect to the factory via the cloud.
The spinning, dye, weaving, cut and sew are all integrated. Vertical integration (in which the supply chain of a company is owned by that company) leads to cost savings which can be reinvested in their facilities.
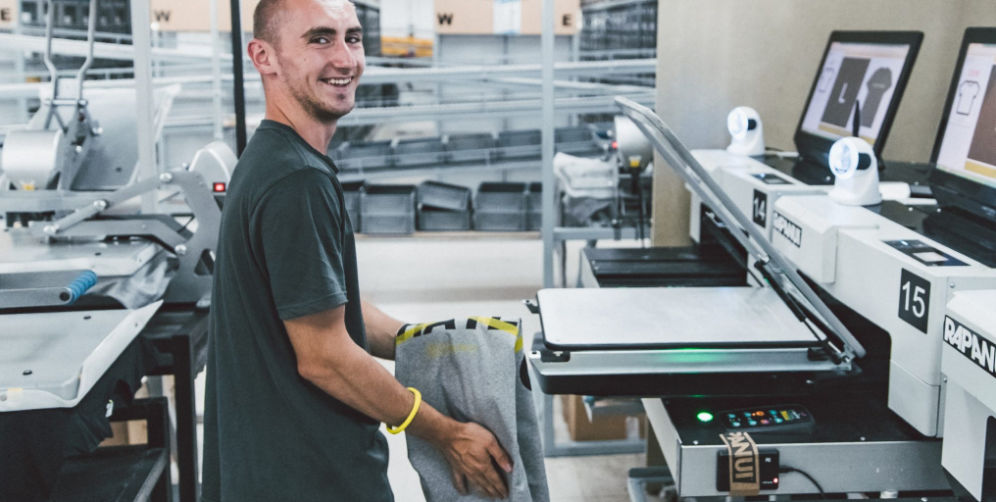
Image from Teemill
Old t-shirts into new
Every product produced by Teemill is designed to be sent back when it’s worn out or the customer no longer wants to wear it. Although the printer ink used is slightly more expensive than normal ink, the composition allows it to be removed more easily. Scanning a QR code in the wash-care label generates a free post label, which can be used to send the garment back to Teemill, earning credit towards the next purchase. Importantly, this keeps the t-shirt, and the value of the materials, within the system.
By rewarding people for keeping the material flowing, we’re changing the way people think about their wardrobe. Rather than waste, they see assets and then some really interesting stuff starts to happen. Because our customer is also our supplier, everybody is rewarded for keeping the material flowing.
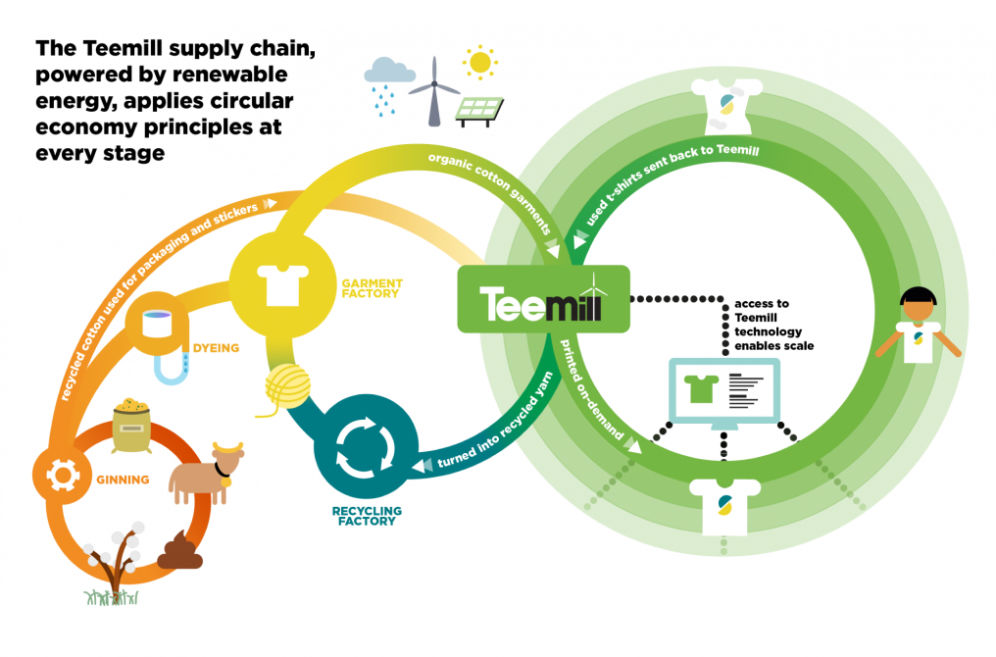
Sign up to our newsletter
Sign up for our monthly newsletter and make sure to tick the “Supply chain” box below to receive the latest updates on circular supply chains.