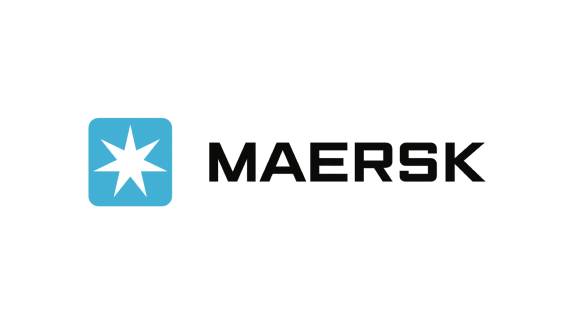
name:
Maersk Line
Maersk Line provide trade and transport solutions, for which a reliable supply of low-cost steel is extremely important. Maersk is exploring how to prepare ships for quality recycling in the design phase, and developing a Cradle to Cradle Passport. The aim is to gain greater control over the materials they use, and ultimately make new ships from old.
The shipping industry is currently reliant on two commodities in particular – fuel and steel. And with steel comprising roughly 98% of the volume of a container ship like the Triple-E, a reliable supply of low-cost steel is extremely important for Maersk Line. As a result, the company is now exploring how to prepare ships for quality recycling already in the design phase, and is developing a Cradle to Cradle Passport as the first step on this journey.
Currently, when the tradeoffs between maintenance and technological improvements are no longer practical or viable, and a Maersk ship is decommissioned, it is taken to a shipbreaking yard in China. Here, the vessel undergoes a safe and certified recycling procedure. However, due to scale of the product and the vast number of different component suppliers, until now it hasn’t been possible to identify different material types and grades during this traditional disassembly process, so the mixed recyclate loses the quality, properties and value of its previous state. Steel that had been found in seven different grades becomes a low-grade, low-price material.
In response to volatility in both steel and fuel prices, Maersk Line have developed a Cradle to Cradle Passport in parallel with the construction of 20 new Triple-E ships, the first of which will be delivered in June 2013. The Passport, a first for the shipping industry, will comprise an online database to create a detailed inventory that can be used to identify and recyclerecycleTransform a product or component into its basic materials or substances and reprocessing them into new materials. the components to a higher quality than is currently possible.
By creating a resource that is flexible, manageable, and can be maintained throughout the 30-year lifetime of a ship, Maersk Line gains an improved understanding of the composition of the vessel that enters the recycling yard. As a result, the materials – including the 60,000 tonnes of steel per ship – can be sorted and processed more effectively, maintaining their inherent properties and hopefully commanding a better price when re-sold.
Ultimately, this is not just about shipping; it is about how we manage steel as a resource globally.
- Jacob Sterling, Maersk Line
This project does not only stand to offer significant benefit to Maersk Line, but has wider influence on the way steel recycling is perceived and dealt with globally, explains Head of Environment & CSR Jacob Sterling. With such huge dependencies on fuel and steel prices, reducing the reliance on iron ore is crucial. Increasing the quality of the recycled steel decreases the amount of virgin iron ore required in manufacturing new vessels, so by leading on the improvement of the scrap metal market, Maersk Line begins to mitigate significant steel input costs. The vision is to be able to manufacture a new hull from old, but in the meantime, this process will make the company more resilient to fluctuating steel prices. In addition, the sale of higher quality scrap metal that is not re-used in Maersk Line vessels can be a source of revenue, offering a hedge against rising steel and fuel costs.
This is a positive step for new builds, but what of the 600-odd container ships Maersk Line currently has in service? Sterling suggests that some of principles of the Cradle to Cradle Passport could be applied to these vessels, by pulling together strands of existing data. A lot of information exists that describes what the ships are made of but this information doesn’t usually make it to the scrapyard. Moreover, the process of repairrepairOperation by which a faulty or broken product or component is returned back to a usable state to fulfil its intended use., maintenance and upgrade over the 30-year lifetime of a ship can mean that the vessel that enters the shipbreaking yard can differ from that on the engineer’s blueprints. However, Maersk Line is exploring whether they can generate more end-of-life value from within this system, and early signs suggest that 60-70% of the volume of materials in an existing ship could be documented.
Those familiar with the Cradle to Cradle philosophy will be aware that emphasis is placed on materials choice and product design. However, this hasn’t been a priority for Maersk Line at this stage. Sterling sees understanding the materials currently used in the shipping industry as an essential step before thinking about substituting materials or re-thinking design. Not only will the Cradle to Cradle Passport enable more useful disassembly and recycling information to be fed back to engineers at the planning and design phase, but if successful, this process will also have a large and vital effect on the way in which steel is arranged globally due to the scale of material under discussion.
The turning point in stakeholder engagement came when our plans went from conceptual to very practical.
- Jacob Sterling, Maersk
The success of the project has depended on stakeholder engagement and understanding, and this was one of the early barriers that Sterling and his team faced. There was a perception that the Cradle to Cradle Passport meant redesigning the entire ship, using new technologies or alternative materials, requiring significant research and R&D investment. However, when key parties were made aware of the gains that could be realised simply taking the practical step of recording the composition of the ship, the initiative received greater internal enthusiasm.
The team behind the Cradle to Cradle Passport knows that there are real technical challenges still to come, but that this process is vital in beginning to build resilience into an increasingly vulnerable linear business model.