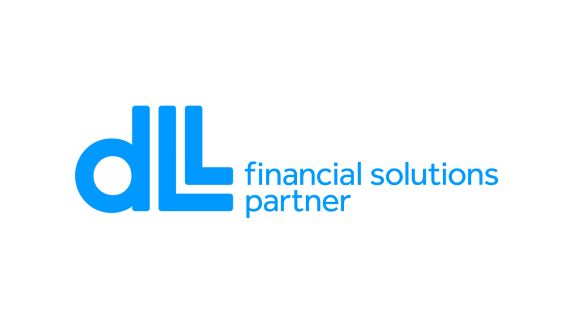
Let’s break down the concept of modular design: essentially, a user can replace one part of a product if it is broken or in need of upgrade, preventing the need to replace the entire device and thereby extending its use. It sounds straightforward, but can be difficult to put into practice.
Seizing the resource and energy benefits of modular design would typically require building this approach into a design brief, and having a suitable business model in place to capture the most value. However, DLL, a global provider of asset-based financial solutions, have had success in applying this innovative way of thinking, combined with refurbishment, to retain the value of a product already in circulation.
Hopefully it won’t happen any time soon, but next time you see an ambulance, take a look at the shape. Many ambulances are made up of two main parts - a large box for patients and medical equipment, mounted on a cabin and chassis that takes care of movement.
DLL are familiar with the way ambulances work, as the company has been operating in the UK healthcare industry for over a decade and is today the leading funder of National Health Services (NHS) ambulances. Many of the funded ambulances return to DLL after a period of five to seven years, and are typically sold at auction.
The company sought to identify why ambulances were returned by the NHS trusts, and found that the main reason was high maintenance costs, especially for chassis components like the engine and gearbox. The rear box, on the other hand, was often in working order. As a result, DLL identified remounting ambulances as a means of maintaining and even increasing vehicle life. By mounting the most valuable part of the existing ambulance on a new chassis (with new engine, gearbox and manufacturer warranty), investment costs for the end customer can be reduced by more than 20% and life of the vehicle is extended by a further five to seven years.
Perceptions of quality, safety and performance have historically hindered the expansion of refurbishment activities. That’s why DLL contracted an external testing company to conduct a series of driving tests on the refurbished ambulance. It passed all tests and has been concluded safe and compliant, which makes the performance of the refurbished ambulance as good as a new one. Particularly in a regulated market like the healthcare sector, this “certificate” is crucial in scaling up remounting activities in the UK.
This project is an important milestone for DLL, as the company plays an active role in the process of extending vehicle life, financing the full cost of the refurbishing process rather than just the end product. Combined with leasing, this enables DLL to take a more long-term approach to vehicle management, extending the lifecycle of an ambulance into a second or third life and joining forces with manufacturers, converters, NHS trusts and even the ambulance drivers.
Demonstrating the benefits of refurbishment to users is one hurdle, but projects like this could also send a message to the wider business world. Healthcare is one sector in which the issues of quality, safety and reliability are paramount. What’s more, the publicly owned National Health Service is heavily regulated compared to other industries in which DLL operate such as construction or agriculture, making remounting relatively more complex. If a new refurbishment opportunity can deliver economic benefits in this challenging context, it’s likely that there are similar untapped sources of value in other sectors.